Mob & Whatsapp: +86-166-5035-8998

Steel Wheel Set
Description:
The steel wheels are essential components for various types of cranes, including overhead cranes and gantry cranes. The wheels are forged from high-quality materials such as 60#, 65Mn, and 42CrMo to ensure durability and performance.
The wheel block is designed with a specialized bearing surface, while the trolley frame, end carriage, and wheel assembly support surfaces undergo precision processing. This design guarantees minimal horizontal and vertical deflection of each wheel, enabling high-precision assembly, smooth operation, and easy replacement.
The wheel block’s bearing support adopts a corner box structure, which is securely fixed to the trolley frame or the crane end beam’s bending plate using bolts. This structure allows wheel adjustments during use and maintenance, ensuring proper horizontal and vertical alignment to prevent rail gnawing. The corner box structure is a widely adopted and proven technology in China, offering reliability and ease of maintenance.
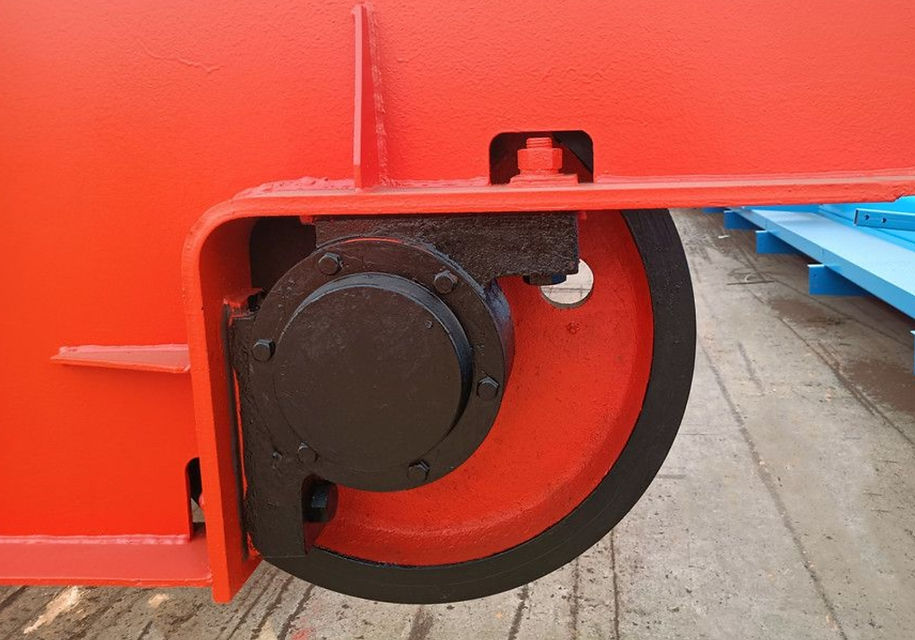
Features:
-
The wheel diameter and material selection are designed to withstand the most demanding operating conditions, ensuring that no part of the wheel is subjected to overload under maximum load-bearing forces.
-
The wheels are manufactured from 65Mn or ZG430-640 (CL60) cast steel, with the tread and inner flange surfaces undergoing high-frequency induction heat treatment. The hardness and quenching requirements comply with the following technical standards:
-
Tread and inner flange hardness: HB 300–380
-
Minimum quenching depth: ≥ 20mm
-
Minimum hardness of the hardened zone: HB 260
-
Welding repairs on the tread or inner flange are strictly prohibited, as they may compromise the wheel's performance and structural integrity.

Parameters:
-
Type: Casting Wheel
-
Applications: Suitable for cranes, trolleys, transfer cars, heavy-duty machinery, port cranes, steel plants, and other industrial applications.
-
Materials: 4140, SCM440, 42CrMo, SSW-QIR, 65# Steel, 65Mn, 50SiMn, QT800, ZG35SiMn, SSW-Q1
-
Dimensions: φ250, φ350, φ400, φ500, φ600, φ700, φ800, φ1000, φ1200, or customized according to customer requirements.
-
Manufacturing Process: Casting
-
Quality Control: Comprehensive quality inspection including Ultrasonic Testing (UT), Magnetic Particle Testing (MT), Radiographic Testing (RT), Penetrant Testing (PT), chemical composition analysis, and mechanical property testing.
-
Heat Treatment: Quenching and Tempering
-
Quenching Depth: ≥20mm
-
Surface Coating: Black oxide coating with rust-proof oil for corrosion protection.
-
Inspection Options: In-house inspection with the option of third-party inspection as per customer request.
-
Standards Compliance: ASTM, ASME, DIN, JIS, ISO, BS, API, EN, GOST
-
Certificates Provided:
-
Raw material certificate (chemical composition report)
-
Heat treatment report
-
Dimensional inspection report
-
Non-destructive testing report (UT/MT)
-
-
Packaging: Seaworthy plywood cases mounted on steel pallets or customized packaging as per customer requirements.
-
Delivery Time: 15–30 working days
-
Competitive Advantage: Comprehensive quality control throughout the entire production process, including ingot smelting, casting, heat treatment, precision machining, and final inspection before delivery.
-
All products are certified with CCC, ISO9001, and CE certifications, ensuring high-quality standards and reliability.


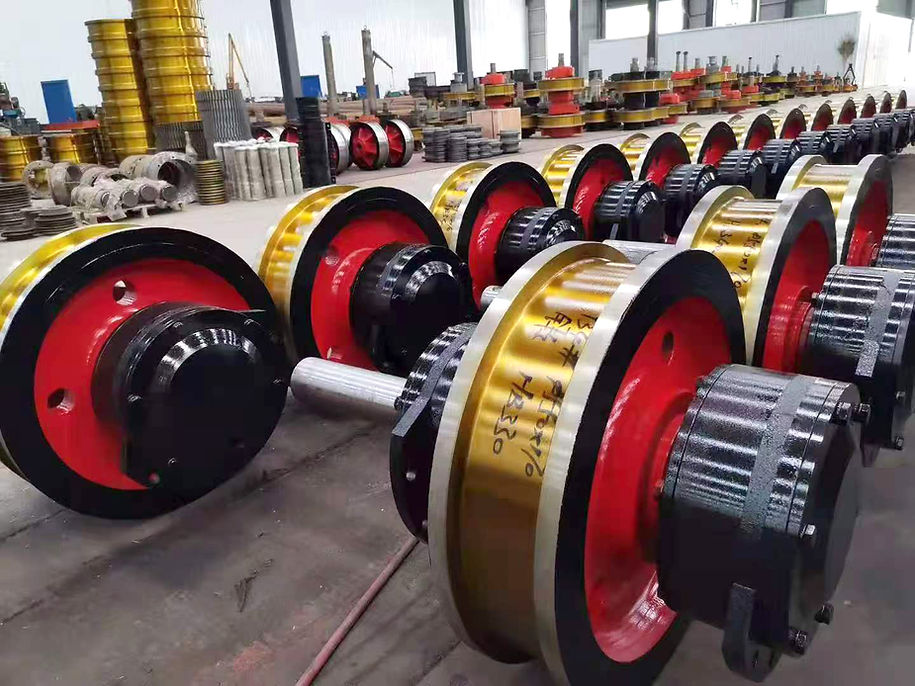

